Advancing residential
construction.
Plant Prefab was founded to make it faster, easier, and more sustainable to build high-quality housing.
We'd spent a decade working with other housing factories, experiencing the drawbacks of conventional modular and panelized systems, and saw an opportunity for innovation. We recruited a team of experts from construction, architecture, and manufacturing and set out to devise a better approach.
The result is an infinitely adaptable panel-based building system, driven by advanced engineering and produced with state-of-the-art manufacturing. It’s a versatile, scalable building solution that flexes to fit diverse project designs and scopes, helping general contractors, architects, and developers deliver housing with industry-leading speed, quality, and sustainability.
Our Story
In 2006 we founded a residential design studio called LivingHomes. We focused solely on residential design for factory construction, partnering with leading architects working to push the limits of sustainable design and advance adoption of prefabrication techniques.
The first home we delivered was the first home ever to achieve USGBC LEED for Homes Platinum certification, with many more to follow. Our projects won awards for design, sustainability, and construction innovation, shattering long-standing stereotypes of prefab construction and redefining the possibilities of factory-built housing. But we worked with ten different factories through the years and found that none were able to consistently meet our needs for design integrity, quality, and sustainability.
We realized that in order to truly achieve our vision—to make it faster, easier, and more sustainable to build high-quality housing—we needed a building solution and manufacturing capabilities designed for this purpose. The idea for Plant Prefab was born.
Read more
⌄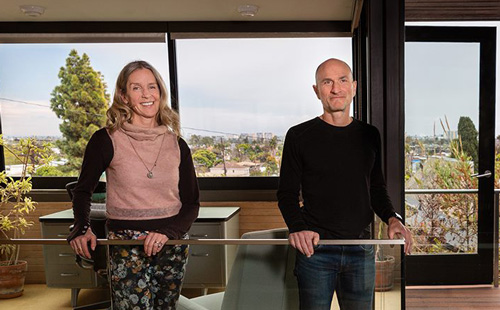
LivingHomes and Plant Prefab founder Steve Glenn with founding team member Amy Sims in the first LivingHome. Designed by Ray Kappe, FAIA, the private residence was the first in the U.S. to achieve USGBC LEED for Homes Platinum certification and was installed in just eight hours.
Carbon-Neutral Operations
We were the nation’s first prefabricated home builder to make a carbon pledge and we’ve achieved carbon-neutral operations since 2020.
Each year we take an in-depth audit of our operations, considering both embodied and operational carbon from primary, secondary, and tertiary sources. Then, we seek ways to continuously reduce emissions throughout our value chain, accelerating the transition to a net-zero carbon economy.
Waste Reduction
In traditional construction, up to 40% of materials are lost to waste. We bring that down to almost zero.
Our industry-leading material efficiency is driven by our advanced virtual design and construction process, which produces a precise list of materials and analyzes it for optimal usage. This allows us to order materials in the most efficient dimensions possible and allocate those materials in the most efficient manner possible. Precision cutting and manufacturing means no spoilage, and the waste we do produce is sorted for re-use or recycling, keeping valuable resources out of the waste stream.
Healthy, Sustainable Materials
Building materials impact a home’s energy performance, indoor air quality, occupant comfort, and carbon emissions. That’s why we carefully evaluate each material we specify, considering product safety, performance, and environmental factors like recycled content and embodied carbon.
Our USDA-certified, bio-based Type X drywall contains 95% recycled content and has the same strength and performance of standard drywall with up to 22% less weight for lower transportation fuel energy. Our exterior sheathing incorporates a water-resistive barrier and continuous foam insulation, so we can use less materials in each project while providing a more durable building envelope that increases energy efficiency. We use finishes with low or no volatile organic compounds (VOCs) and categorically avoid products with known carcinogens.
Leadership
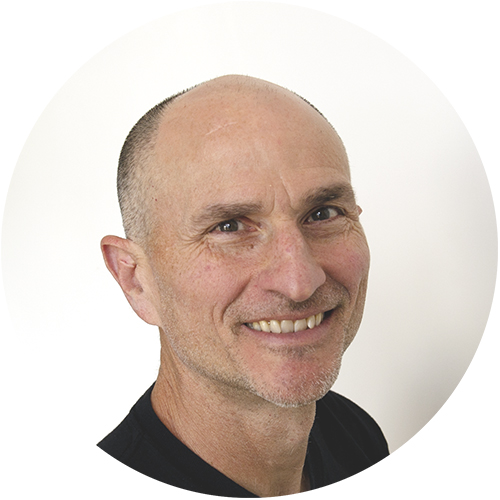
Steve Glenn
Founder, CEO & Chair of the Board
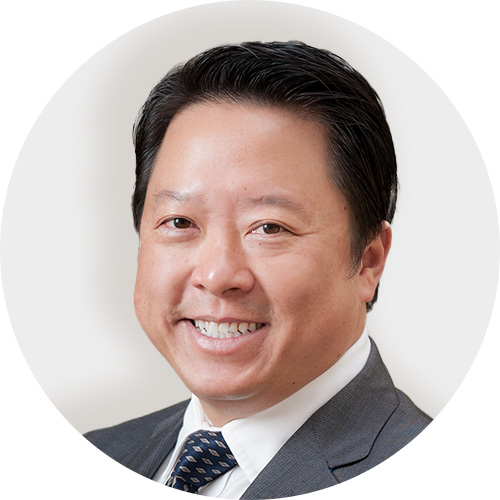
Stephen Jordan
SVP of Business Development & Marketing
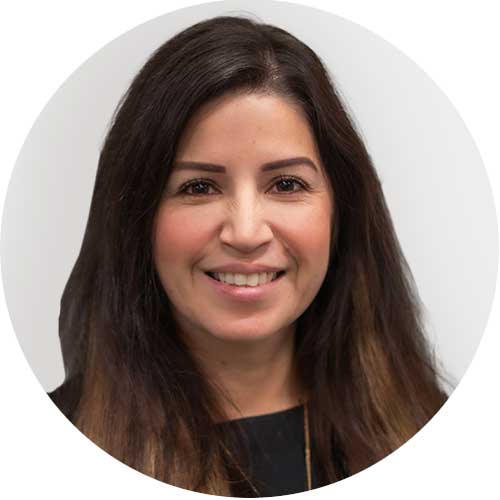
Lizeth Tiscareno
VP of Business Operations
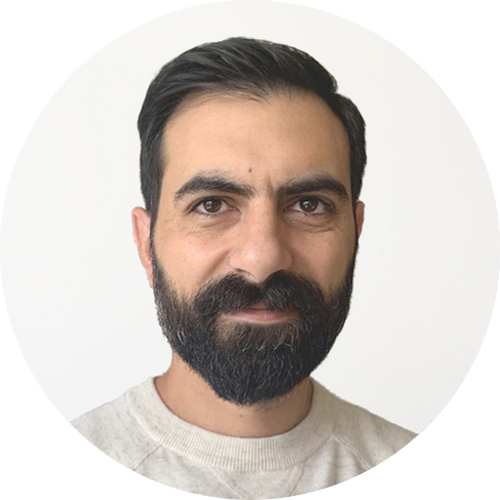
Monder Shoufany
Director of Design & Project Management
Board of Directors
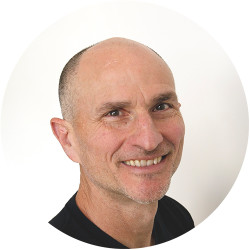
Steve Glenn
Founder, CEO & Chair of the Board, Plant Prefab
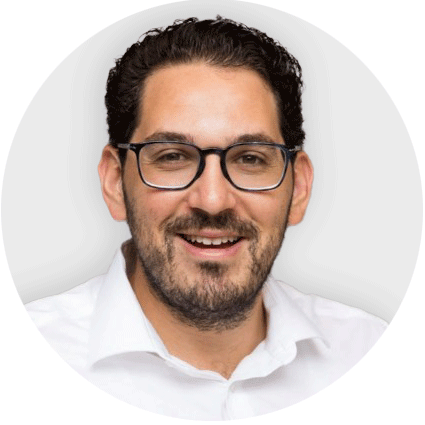
Michael Mann
General Partner, Anchor Capital
Join us.
If Plant’s values resonate with you and you’re interested in reinventing the homebuilding industry, we’d love to hear from you. Diverse perspectives and forward-thinkers welcomed.
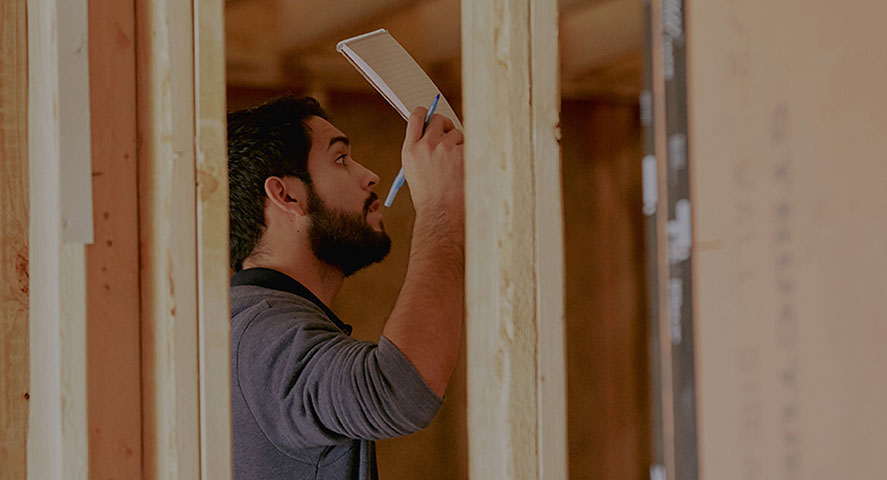
Safety
Employee health and safety is our #1 priority across all facilities. Our Occupational Health and Safety Management System and protocols extend beyond industry standards, and we have a dedicated committee that meets weekly to review metrics and practices.
We foster a culture of safety awareness that encourages employees to play an active role in creating a safe work environment, including reporting hazards and offering suggestions for improvement. Instead of punitive action for mistakes, we focus on preventative action through awareness. Our best-in-class safety record is a direct result of this constant focus on risk mitigation and employee well-being.
Benefits
As a socially responsible company, Plant Prefab offers competitive compensation and excellent benefits. We also invest in our staff with continuous training and opportunities for professional development, helping workers grow with the company.
All regular, full-time employees are granted stock options and are eligible for annual bonuses as well as full healthcare, vision, and dental coverage. Production staff receive paid time off and holiday pay. They are provided with all the tools required to perform their job, as well as extensive safety training, a comfortable break room, and many other amenities not found in conventional construction.
Training & Development
We know that nothing is more critical to our success than a safe, skilled, and satisfied team, so we invest in our employees with continuous training and development.
Production staff receive extensive safety training, ranging from injury and illness prevention to materials handling. Ongoing certifications and cross-training programs empower workers to learn a new trade, providing expanded opportunities within and beyond Plant Prefab. We help all workers grow with the company by promoting from within whenever possible.
Awards

First LEED for Home
Platinum Rating

Energy Value Housing
Gold Award (NAHB)

AIA Top Ten
Green Projects
Award
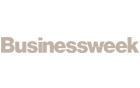
Top Ten Buildings
of the Year
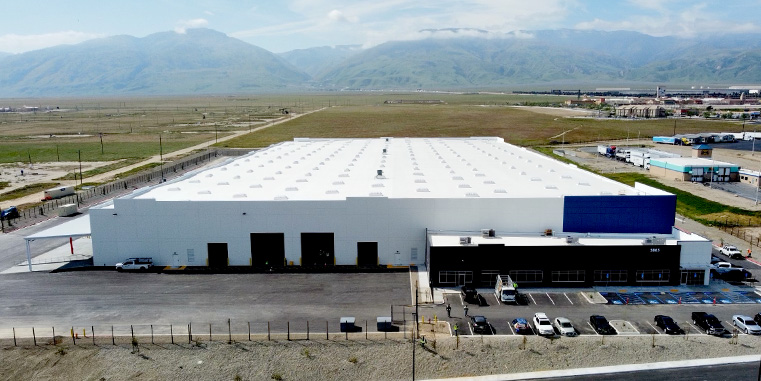