PLANT BLOG
What Is the Cost to Build a Prefab House?
All the Expenses You Should Expect and How to Determine Your All-In Costs
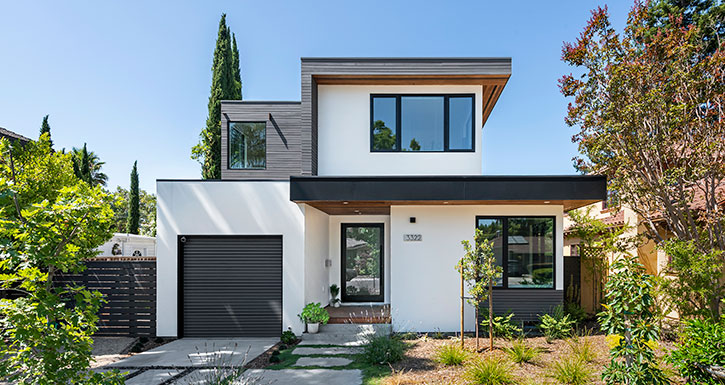
The number one question we receive is, "How much do Plant homes cost?" It makes sense, given that many people think about prefab homes as a set product.
If every prefab home was an identical structure with an identical design, installed on an identical lot in an identical city, then this thinking would absolutely apply. But the real world isn't so cookie-cutter: each location has a unique climate with specific building and zoning codes to suit it; each lot has different topography, soils, and site access conditions; and of course, each client has their own design ideas (and budget) for the kind of home they want to create. From Midcentury Modern to Craftsman cottage, restrictive urban zoning to wide open desert, no two projects are even close to the same.
While many aspects of homebuilding do have straightforward costs (like materials), there are a number of variables that combine to determine the overall cost of a residential construction project. This article explains the costs involved in building a prefab home with Plant, and how we help you pull it all together into one tidy estimate.
Factors That Affect Cost
For the purpose of this article, we’ll bucket all the various homebuilding factors and expenses into three main categories: design, lot, and location.
Design
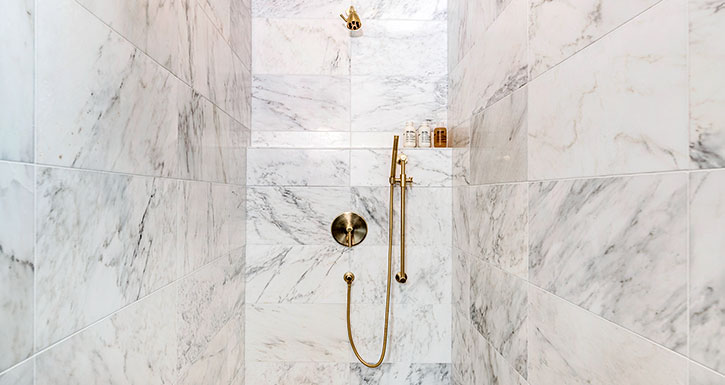
Finishes like tile, flooring, and siding vary wildly in price, so the selections you make will drive your project costs.
Let’s consider “design” an umbrella category for everything pertaining to what is being built:
Home size: How much house are you building?
Obviously a 5,000-square-foot home costs more to build than a 500-square-foot accessory dwelling unit, but specialized spaces like kitchens and bathrooms also cost a lot more than simple spaces like hallways and bedrooms. To understand your costs, you’ll need to hone in on both your square footage as well as the distribution of that space (especially kitchen size and features and the number and size of bathrooms).
Finish specification: What’s included in your house?
This considers both the quantity of fixtures needed to outfit all those rooms (and the linear or square footage of finishes like cabinets, flooring, and millwork), as well as the finish grade. With incredible price variation for nearly every option—an oven can be $300 or $3,000; tile can be $3 or $30 per square foot, and so on—finishes play a significant role in determining the price of a home.
Design services: How much work is needed to design your home and satisfy local code requirements?
Every residential construction project requires design services—even if you’re using a “standard” design (that is, a ready-made design). That’s because the design must be adapted to meet your municipality’s local building code (which specifies things like snow load, fire resilience, and seismic requirements) and your specific lot (which dictates the design and construction of the foundation, among many other things). Then, those updated plans must be engineered, permitted, and translated into construction drawings. Architects and designers manage this process and charge hourly for their time.
As you’d expect, hiring an architect to design a bespoke home from scratch will cost a lot more than the “standard design” process described above. So your desired degree of customization, together with the unique requirements of your lot and location, will drive your design costs.

Lot
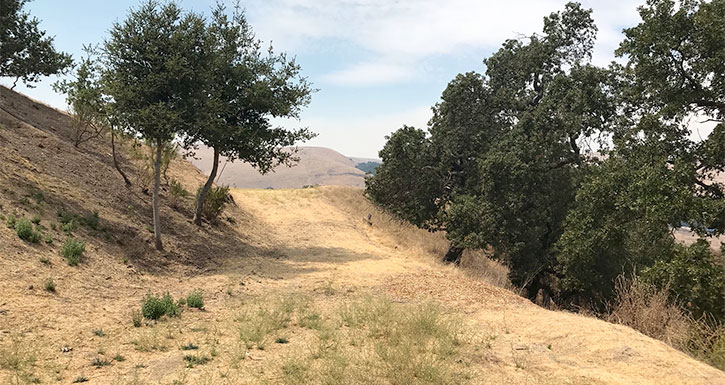
Dreaming of building in a remote locale? Be prepared for significant extra site costs to build out utilities and other required infrastructure.
We’ll use “lot” as an umbrella category for everything pertaining to site work:
Grading & Excavation: How much work is required to prepare your lot for a home?
A flat lot with good soils will need much less work than a sloping lot that requires the construction of retaining walls, or a lot that needs a drainage system to address runoff issues, etcetera. No two lots are the same, and depending on what’s needed for your specific lot, site prep can add significant expense to an otherwise simple project.
Utilities: How much work is required to run utilities?
If building in an undeveloped area, you’ll need to run utilities to your lot. Less work will be required for lots that already have water, sewage, and electrical connections.
Foundation: What foundation is needed, and how much work is required to build it?
Both the design of your home as well as the layout and soil composition of your lot will determine what kind of foundation you’ll need. Size, materials, and the complexity of the foundation design will determine the amount of work required to build it.

Location
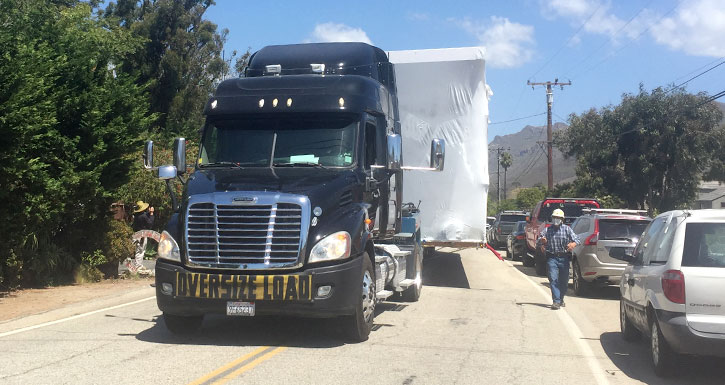
When it comes to shipping, every mile counts. And yes, size does matter.
We’ll use “location” as an umbrella category for everything pertaining to where the home is built:
Transportation: Where is your lot in relation to our factory?
The prefabricated components of your home (typically a mix of Plant Modules and Plant Panels) must be trucked from our factory to your job site, via roads that can accommodate such loads. The further the distance, the higher the cost. Municipalities along the route may also require special permits and escort vehicles, adding to the cost.
Installation: How will your home be installed?
A crane or lift will be required to assemble the prefabricated components of your home on your foundation. The size and design of the home, together with the layout of the lot, will determine the size and type of equipment that will be required.
Access limitations: What’s required to meet access limitations?
Things like steep grades and tight turns along the transportation route, as well as power lines, closely-abutting structures, trees, and other obstructions near or on the jobsite will dictate how the home can be prefabricated (the size of the prefabricated components), how it can be delivered (the size and type of truck and trailer), and how it can be installed (the size, type, and positioning of the crane). These limitations play a key role in determining your transportation and installation costs. For some perspective, a one-day crane rental can range from $3,000 - 25,000 depending on the size and type of crane required.
Local labor rates: What is the cost of skilled labor in your area?
A local general contractor (GC) will manage all site prep and final finish work. The cost of skilled labor varies greatly from one area to the next, and spikes in demand (due to typical seasonality as well as events like wildfires) will further affect the rates charged by local contractors.
Permits and taxes: What are your area’s taxes and permit fees?
Taxes and permit fees are set at the local level and vary greatly from one municipality to the next.

How to Estimate Your All-In Costs
If all of this feels overwhelming, don’t worry; Plant has a detailed yet straightforward process for estimating your total project costs before many of the above-listed specifics have been determined. We call it a rough order of magnitude (ROM) estimate, and we create it as follows:
Gather all available information.
We’ll help you hone in on the size and kind of home you’re hoping to build as well as your anticipated finish specification. We’ll also conduct a feasibility analysis of your lot to identify any major site limitations and get a sense for the project’s transportation and installation needs.
Estimate project scope.
Following your guidance on your desired home design, we’ll make assumptions about the amount of work required to create (or finalize) your design, the amount of site work required to accommodate the home, the amount of materials required to build the home, and approximately how that work will break out between Plant and your general contractor.
Populate costs with historic averages.
For each line item, we’ll fill in cost estimations using historic averages for project designs, lots, and locations similar to yours. Though these figures will shift once a soils report has been completed for your specific lot, they provide a reasonable ballpark for discussion.
Once we’ve filled in all the blanks, we’ll share our estimate and set up a time to review it with you. We’ll make sure you understand all the assumptions and how we’ll help you refine the numbers as we move through the design and preconstruction phases of your project. At this point you’ll have the comprehensive “all-in” cost estimates you need to make an informed decision about building your home with Plant.
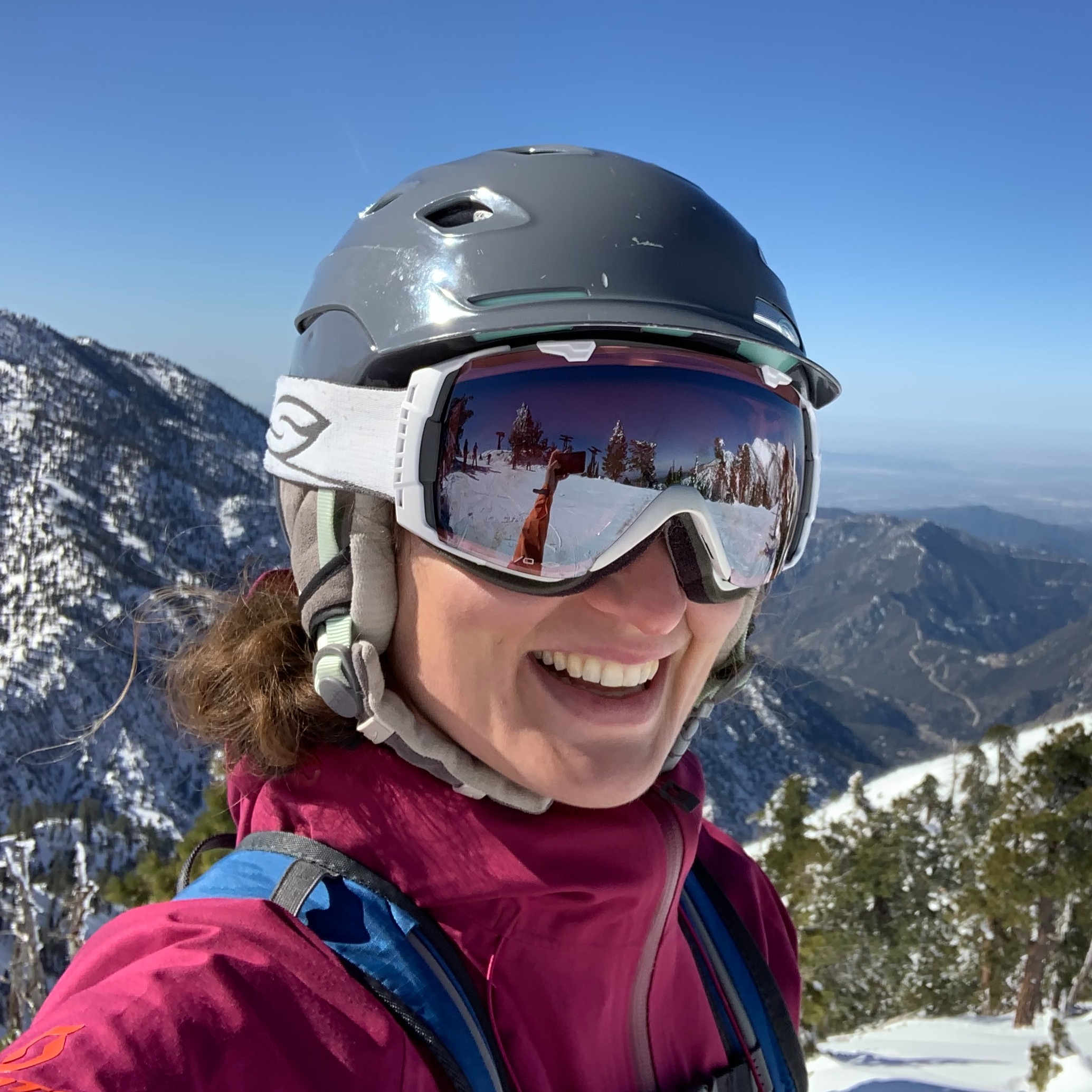
ABOUT THE AUTHOR
Cara Rudio is Plant's Marketing Manager, working to spread the word about building smarter, faster, and more sustainably with prefab.
Contact Us
Learn how Plant can help you build a higher-quality home, faster and more efficiently than any other builder.
Join Our Newsletter
Sign up for our monthly newsletter to receive new posts, news, and more.
LEARNING CENTERLearning Center